New challenges underground
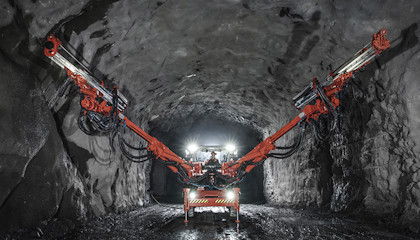
Mining and rock excavation underground face the challenge of improving both productivity and safety. Artificial Intelligence can be part of the solution.
Today the mining industry is under increasing pressure to supply more minerals to meet the needs and expectations of a rapidly rising world population. This often requires extracting from greater depths, which in turn can create challenges when equipment needs servicing or repair.
“Identifying maintenance requirements before something breaks down enables us to make major direct savings in costs and time,” says Patrick Murphy, President of the Rock Drills & Technologies division at Sandvik. That is why Sandvik is working with IBM to introduce advanced analytical cognitive data processing and modeling based on data generated by sensors on loaders and trucks.
“OptiMine® Analytics, partnered by IBM Watson IoT [Internet of Things] solutions, offers our customers a more complete view of their operations for smarter, safer and more productive working,” Murphy says.
Data-driven maintenance is by far the best method.
The principle is that OptiMine® Analytics transforms data into process improvements using the analytics functions of IBM Watson IoT. This information management system allows mining companies to combine equipment and application data from disparate sources in real time, analyzing patterns in the data. Everything is focused on improving availability, utilization and performance.
Jan Ekstrøm at IBM also highlights preventive maintenance as a key to more cost-efficient mining.
“If you organize maintenance into a specific plan, you will always know if you have done too little [because] you get problems with your equipment,” he explains. “But you won’t know if you’ve brought in too much maintenance, which, of course, isn’t cost-efficient either, because all maintenance costs both time and money. That’s why data driven maintenance is by far the best method.”
Mining companies combine equipment and application data from disparate sources in real time, analyzing patterns in the data.
One goal of preventive maintenance is to minimize the number of emergency shutdowns and so prevent the huge costs that arise from such shutdowns. In addition, reducing the risk of emergency shutdowns also improves operational safety.
“Certain mechanical breakdowns can result in personal injury, and it may take considerably more resources to repair a vehicle in a hard-to-reach location than if it can be parked in a workshop as part of a planned maintenance scheme,” says Ekstrøm.
Providing all employees with sensors that continuously measure different aspects of the environment is another solution that can improve underground safety. The system automatically triggers an alarm if there is any indication of hazards in the working environment.
“This type of solution requires expanded communication networks that are able to link together activities below and above ground. It’s even more of a challenge now that mining is taking place at lower and lower levels.”
To meet this challenge Sandvik has acquired Newtrax, a digital mining technology provider. The acquisition will help Sandvik create conditions for establishing an IoT network in a range of mining environments and for obtaining real-time information from the devices and equipment used in mines.
The system automatically triggers an alarm if there is any indication of hazards in the working environment.
Sandvik and IBM clients such as Petra Diamonds and Barminco are using IoT to reduce miner exposure to hostile work environments and to increase safety. OptiMine® Analytics is scheduled to be used by Vedanta Zinc International’s Black Mountain Mining (BMM) operations in South Africa’s Northern Cape Province, to accelerate data-driven operations for safety, efficiency and productivity for trucks, loaders and drills.
Additionally, Hindustan Zinc, one of the world’s largest producers of zinc, lead and silver, has tapped Sandvik to implement a major digital transformation at its Sindesar Khurd Mine in India. The aim is to ensure that all required infrastructure and platforms can achieve world-class mining safety, efficiency and productivity.